Success is measurable - Customer success stories
Discover how customers have used our products for lubrication.
Optimise your work processes
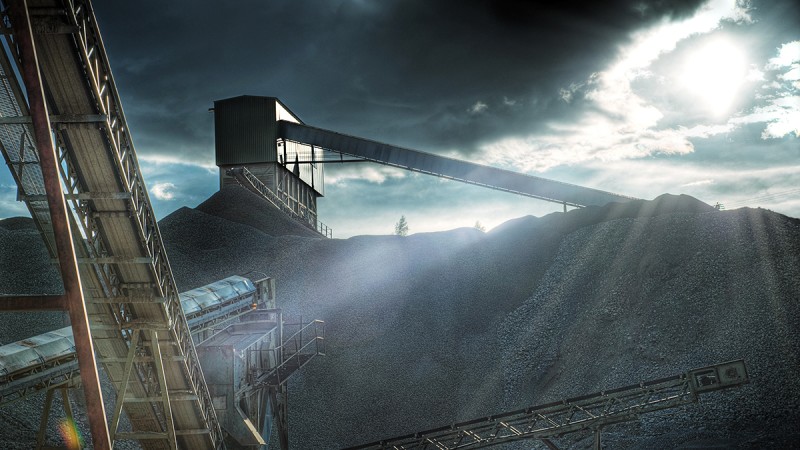
Mátrai Erőmű Zrt., I Hungury
... and conveyor belts will run smoothly
Tough and contaminated environments - Are suitable automatic lubrication systems available?
The Hungarian power plant and open-cast mine Mátrai Erőmű Zrt can answer this question with a definitive “YES”.
The solution is simple
Instead of relying on manual lubrication for the transportation of coal, the power plant operator switched to automatic lubrication at his plant in Visonta. First of all, 100 CONCEPT8 lubrication systems were installed on the kilometre-long belt conveyor system, which now ensures a reliable supply of lubricant to all drums and rolling bearings. The automatic systems lubricate precisely, in metered quantities, and can supply up to 8 points with the correct amount of grease. Overgreasing is virtually ruled out.
The conclusion
The demanding work associated with manual relubrication and time-intensive repairs has been significantly reduced. The simple operation of the lubrication system has proved just as convincing to the customer as the robustness of the system. As a result, Mátrai Erőmű Zrt has been using a further 30 CONCEPT8 lubrication systems for the belt drums since 2016.
Satisfied with the CONCEPT8 lubrication system, the power plant operator is introducing further lubrication systems in 2019, this time in the form of CONCEPT2 for the lubrication of drive motors. 35 lubricators have already been installed and a further 15 will be added.
Are you looking for a solution for your system? We will be happy to advise. No obligation. Straightforward. Reliable.
Lower your costs
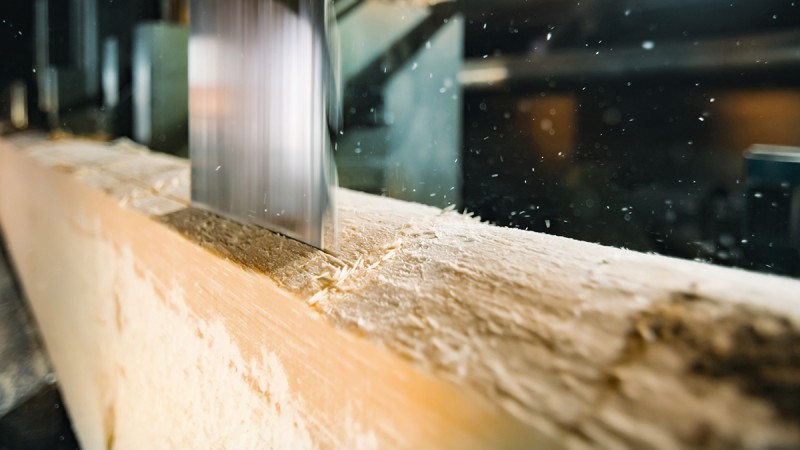
anonymous
... manual lubrication is a thing of the past
Manual lubrication versus automatic lubrication - Are you using the right grease?
In lubrication terms, wide belt grinding machines count among the so-called critical assemblies used in the wood-processing industry. In accordance with the maintenance contract and for reasons of safety, these may only undergo manual relubrication while stationary. However, frequent machine start-ups (following machine stoppages for lubrication) lead, in this particular case, to thermal overloading of the grease, which gives rise to poor grease distribution and undesirable bearing failures.
The solution
Wide belt grinding machines can also be lubricated during operation using automatic lubrication systems. Instead of the previously used lubricant containing bentonite thickener, the plant operator switched to a lubricant which is more suitable for use in high-speed spherical roller bearings.
In short: the bearings are always supplied with the optimum amount of lubricant. By switching to a lubricant with a better base viscosity, the risk of overheating is reduced.
Benefits
The plant operator saves several thousand euros a day, as the reputed plant downtime caused by the failure of the wide belt grinding machine is drastically reduced. The accident risk faced by employees is also reduced as a result of the changeover.
Are you looking for a solution for your system? We will be happy to advise. No obligation. Straightforward. Reliable.
Lubrication can be performed everywhere
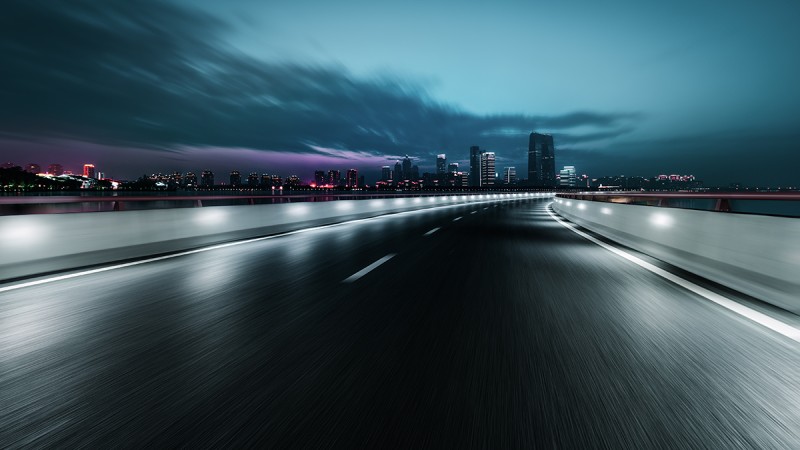
BMW I Germany
... we even have solutions for the Automotive Sector
Fresh air on the paint line is a must - This is how BMW prevents large fan failures
Regardless of the assembly involved, the following is beyond dispute: too much is not a good thing, but neither is too little. This is why correct metering is important.
In this particular case, it was the large fan on the paint line that was lubricated “too well”. The consequences of this: temperature overload and premature failure of the bearings.
The solution
Switching from manual lubrication to automatic lubrication with just one lubrication system ensures that all of the fan's lubrication points are continually supplied with the right quantity of lubricant at all times.
Satisfaction down the line
Maintenance work is reduced by approximately 5.5 hours per month and shift work is running almost seamlessly. Reason enough for automatic lubrication systems to be used with other critical assemblies at BMW.
Can the solution be transferred to other assemblies?
“Yes” is the categorical answer from Schaeffler. The compact automatic lubrication systems from Schaeffler can be used for pump motors, fan gearboxes and many other assemblies. Individual requirements? No problem. There is always a solution.
Are you looking for a solution for your system? We will be happy to advise. No obligation. Straightforward. Reliable.
Plan ahead
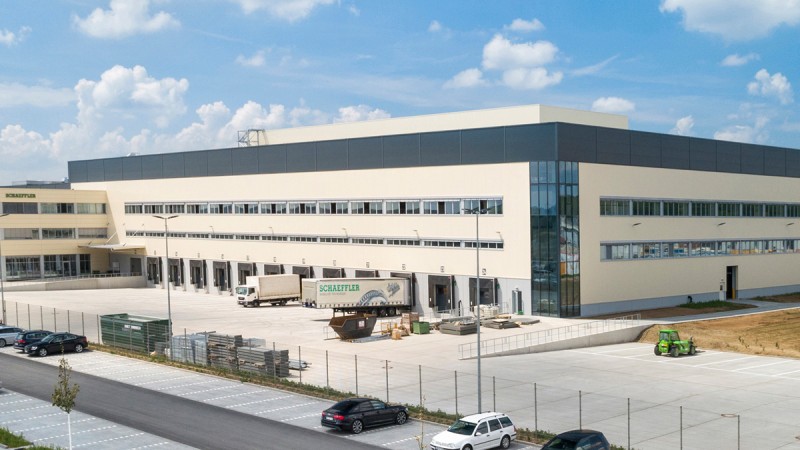
Schaeffler I Germany
... for hassle-free operations in your logistics centre
What are the benefits of automatic lubrication in the field of intralogistics?
Egon Grief, Head of Maintenance for EDC Central at Schaeffler, has the answer:
What does a “big” solution look like?
169 lubrication pumps, 162 Y distributors, 323 progressive distributors, 556 splitters and approx. 45 km of lubricant lines with 2,500 lubrication points supply approx. 12 km of conveyor chains for drive and transport purposes.
Is investment worthwhile?
Schaeffler's answer to this question is a definitive “yes”, on both a small and a large scale.
Schaeffler itself made an investment in the six-digit range. After just one year, the investment has paid for itself, the maintenance outlay has been reduced by 2,000 hours a year and the risk of injury during maintenance work has been significantly reduced.
Are you also looking for a solution for your machine? We would be happy to advise you without obligation and in an uncomplicated manner.
Contact & references
Discover more about our testimonials and solutions. Simply contact us!
Are you looking for a Condition Monitoring solution? Then these testimonials may be of interest to you.